|
 |
Sitemap |
 |
FAQ |
Welcome to Anber Powder Coating Co., Ltd's website! |
|
|
Powder coating lines
Components of powder coating line
|
|
Perforated metal mesh powder coating line
-
Loading area for perforated metal mesh powder coating line
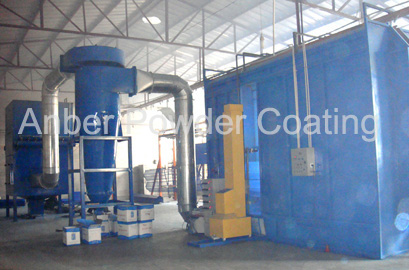 Powder spray booth for punched plate powder coating line
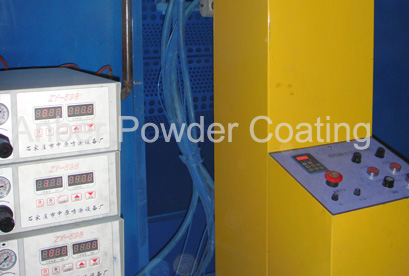 Spray gun and reciprocator for perforated sheet powder coating line
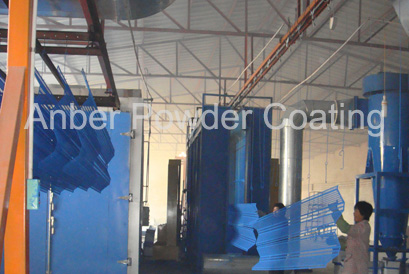 Unloading area for punched sheet powder coating line
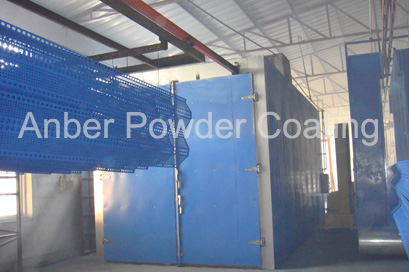 Cooling area for metal mesh powder coating line
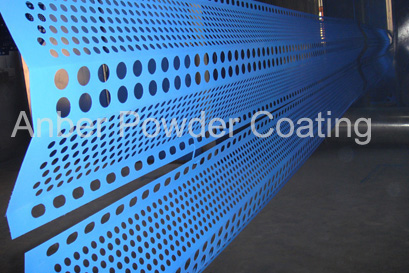 PVC coated perforated metal mesh
Design basis of perforated metal mesh powder coating line
1. Name of workpiece: Perforated metal mesh
2. Max hanging size on each hanger: L3500mm×W150mm×H1200mm
3.Load capacity on each hanger: 2pcs per hanger
4. Suggested interval between 2 hangers: 500mm
5. Conveying speed: 1.3m/min
6. Output: 35-45pcs per hour
7. Spraying method: 4 auto spray guns (match on 2 reciprocators) & 2 manual spray guns
8. Heating source: natural gas (Other choices are available: electricity, oil or coal)
9. Pretreatment system: Immersion tank type
10. Required plant size: L52m×W24m×H6.5mm
Design description for perforated plate powder painting line
1. According to the shape of perforate metal mesh, we design the pretreatment to be economical immersion tank type with 6 stage processings.
2. After chemical cleaning, he pre-treated workpieces will be conveyed to drying furnace for water removal on their surface. The drying furnace is designed being tank type to match with immersion pretreatment tanks, and with a top-door design for easy access of pre-treated workpieces.
3. After drying, the workpieces are ready for powder particle adhesion. Please manually feed them on auto powder painting line. For a better painting result, the spray booth, waster powder recycling system, reciprocator adopts advanced equipments in China through our careful selection. And the spraying guns, both auto and manual are imported from foreign famous company for a longer service life. Then these workpieces will be sent to gas-fired furnace tunnel to let powder melt into a smooth coating.
Process flow for punched metal mesh powder coating line
1. Feed your iron perforated metal mesh on crane hanger for the preparation for chemical cleaning
2. Pre-degreasing stage (50-65 Celsuis for 1 min)
3. Degreasing stage (50-65 Celsuis for 2 mins)
4. Rinsing stage (Room temperature for 1-2 mins)
5. Surface conditioning stage (Room temperature for 1 min)
6. Phosphating stage (35-45 Celsuis for 3 mins)
7. Rinsing stage (Room temperature for 1-2 mins)
8. Drying off oven to remove surface moisture (100-120 Celsuis for 10 mins)
9. Manually transfer the pre-treated objects to powder coating line
10. Powder application with spray guns
11. Powder curing (180-200 Celsuis for 20 mins)
12. Finished product discharging
If above parameters cannot meet with your strict coating need, please contact us for more detail. We can make some adjustments or even improvements to suit your actual production conditions.
Related keywords of punched plate powder coating line
Perforated metal mesh powder coating line, Perforated metal mesh powder painting line, Perforated metal mesh powder spraying line, Semi powder coating line for perforate metal mesh, Punched metal mesh powder coating line, Punched plate powder coating line, Punched sheet powder coating line, Punched panel powder coating line, Perforated plate powder coating line, Perforated sheet powder coating line

|
|
|